Powder Coated Electrical Enclosures
If your enclosures or fabricated component parts require high quality durable powder coat finish, Bison ProFab has the facility, equipment and skilled personnel to provide that service. Properly applied powder coat finishes are very resistant to cracking and peeling and provide extremely high abrasion, corrosion and chemical resistance. Powder coatings typically meet or exceed the finish performance characteristics of conventional solvent-based wet coat finishes.
Bison ProFab follows a documented process from material preparation, through powder coat application and proper curing of the finish coat. You can download a copy of this process here.
What is Powder Coating?
Powder coating is a durable, attractive and effective finishing option for most metal surfaces. Powder coating offers many advantages over traditional liquid enamel or acrylic finishes – and it’s also very cost effective.
State of the art powder coating equipment and trained craftsmen ensure premium finish quality. Bison ProFab used the new OptiFlex2 – the world’s most advanced manual powder coating technology. This equipment allows us to spray all powders with ease, coat complex geometries with outstanding efficiency and quality. The high performance integrated cascade power supply, with 100,000 volts of first pass power, efficiently charges all types of powder. The spray guns PowerClean technology cleans the entire powder path from the pump to the gun tip. Using powerful blasts of air, OptiFlex2 improves performance even when spraying a variety of powders.
Technology
State of the art GEMA OptiFlex2 equipment, long recognized as a worldwide leader in paint system equipment. The revolutionary OptiFlex2 spray system provides unrivaled operator control.
Benefits
Powder coatings are among the most durable finishes available. Bison ProFab’s highly skilled technicians are capable of meeting the most stringent coating standards. Powder coatings incredibly efficient paint transfer and retention provide an exceptionally cost effective investment.
Environmentally Friendly
Excess paint overspray is recovered. Applied as a dry powder, without solvents or chemical fillers, powder coating emits near zero volatile organic compounds. With no solvents, thinners or hazardous waste, you can feel comfortable knowing your project has minimal environmental impact.
Capacities
- Spray Booth: (Inside Dimensions) 10’ High x 9’8” Wide x 15’ Deep
- Batch Oven: (Inside Dimensions) 10’ High x 10’ Wide x 15’ Deep
Gas fired w/ maximum operating temperature of 450 degrees F
Surface Preparation
- Proper material/surface preparation is the most critical process that will ensure optimum powder coating adhesion and long-term paint performance. Bison ProFab uses two different types of surface preparation – and sometimes, a combination of the two.

Chemical Washing
One of our methods of surface preparation, prior to powder coating, is chemical washing. Chemical washing removes surface contaminants such as fine dusts, oil compounds and other imperfections that would reduce paint adhesion and performance. Our second method of surface preparation is blasting. Many of you have heard of sand blasting – but we use a more modern technology called dustless blasting.

Dustless Blasting
Dustless blasting is the world’s fastest, most cost effective and environmentally friendly surface preparation tool. It does everything a sandblaster can do – but it does it better! How does dustless blasting work? Water and media are mixed in the blast tank and during the blasting process, water encapsulates the abrasive and the coating being removed – preventing them from becoming airborne. The particle droplets fall to ground, keeping surrounding areas clean. The water adds mass and energy, making Dustless Blasting more powerful than dry blasting. The addition of a rust inhibitor prevents flash rust for up to 72 hours.
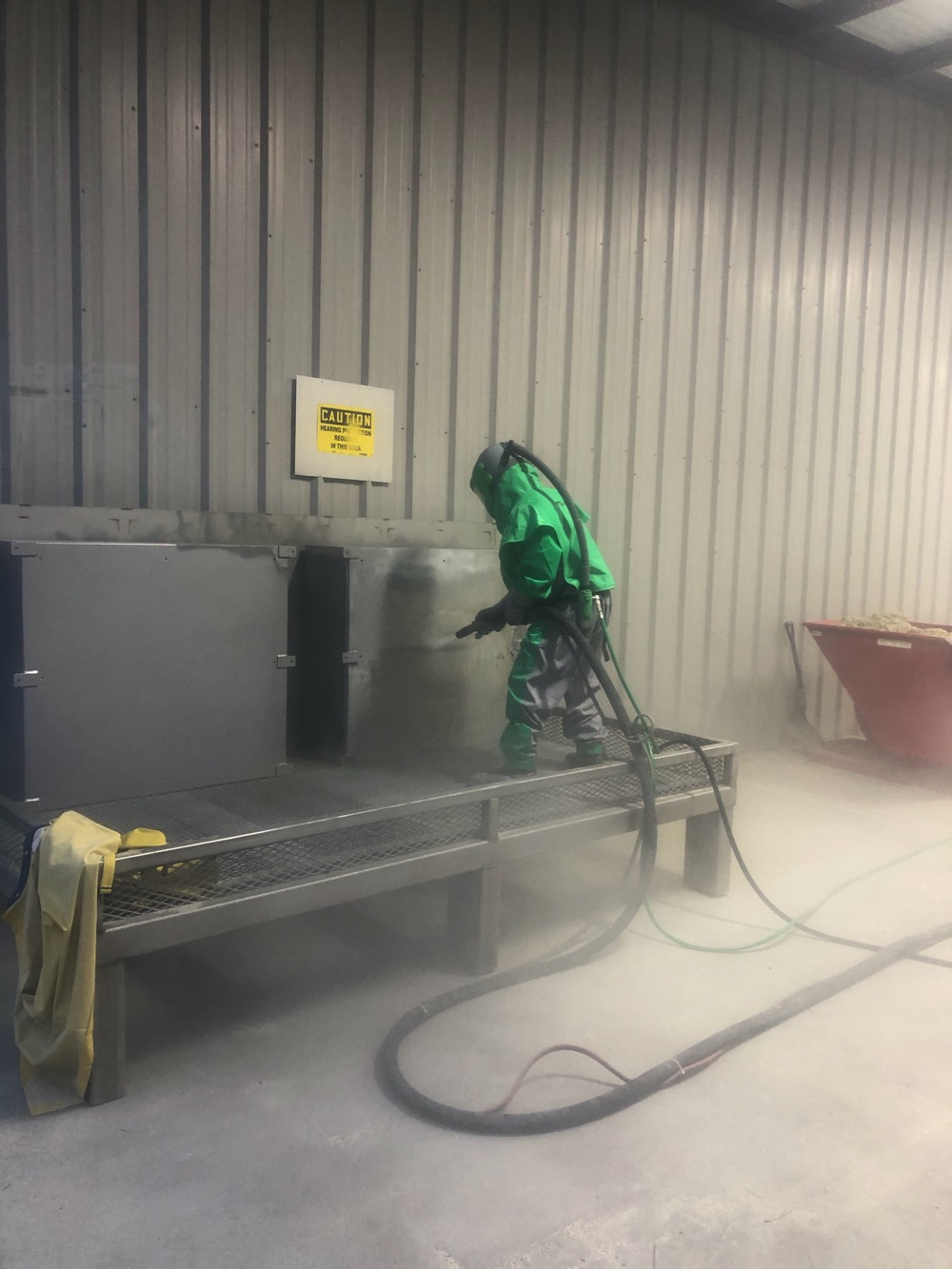